The Global Motor Monitoring Market size is expected to reach $3.1 billion by 2027, rising at a market growth of 7.3% CAGR during the forecast period.
Motor condition monitoring is a system that uses data collected from electric motors and rotating equipment to identify flaws before their occurrence. Rotating machinery and electric motors are the devices that consume the most electricity. Motor monitoring allows for the prediction of potential motor failures and the intervention of the failure in advance. Condition monitoring helps to avoid unplanned downtime while also increasing the energy economy. Additionally, motor condition monitoring also prevents the cost that occurs in unnecessary maintenance of the motor.
Condition-based maintenance majorly focuses on preventing excess downtime, asset failures, and wasteful practices by monitoring the health of the motor to identify what maintenance needs to be performed and when. Any predictive maintenance approach is expected to be incomplete without it. Motor monitoring makes sure that maintenance is only being undertaken when particular thresholds are met or indicators exhibit symptoms of declining performance or impending failure.
Predicting impending motor breakdowns necessitates knowledge, experience, and the use of as many tools as possible. The more tools a technician has and knows how to utilize, the more equipped they is expected to be to estimate the longevity and health of the motor. Online monitoring and offline testing are two aspects of motor monitoring that must be examined and completely utilized in order to acquire an adequate diagnosis of the motor's condition.
The motor itself contains a variety of components that must be precisely tested, including insulation systems, copper winding wire, bearings, and other electrical and mechanical elements. The insulation system comprises very thin insulation produced onto the magnet wire or winding while the ground-wall insulation safeguards the magnet wire in the slots. Off-line testing equipment can accurately analyze the health of these insulation systems, and when the data is appropriately displayed, it can help in anticipating the motor's ability to remain in operation, as well as the requirement of any type of maintenance in the motor.
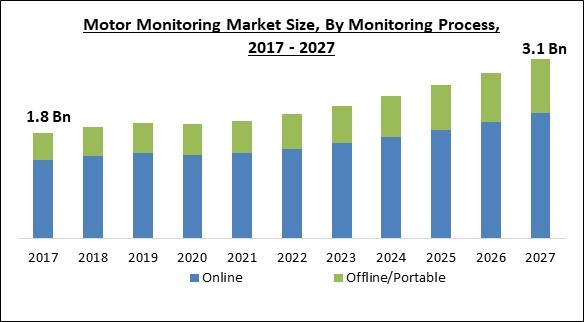
The outbreak of the COVID-19 pandemic severely impacted worldwide economies. The closure of various plants and factories, due to lockdowns that were enforced by governments to regulate the spread of the infection, had a severe impact on supply chains across the world, negatively affecting manufacturing, delivery schedules, and product supply. Various companies already stated that there may be delays in product deliveries and a drop in future production. Additionally, worldwide travel prohibitions implemented by various countries across all the regions are affecting opportunities for commercial cooperation and partnerships.
In addition, the pandemic also harmed the motor monitoring industry in a severe manner. Governments and municipal agencies imposed stringent regulations, due to which all non-essential activities were halted. Due to a lack of focus on the development of end-user industries, this had a negative impact on motor monitoring.
Predictive maintenance is becoming more widely recognized as one of the more easily controllable digitalization applications. Predictive maintenance is a technique for forecasting when equipment will fail and repairing or changing the component before it breaks. This helps to reduce downtime and extend the life of components. Predictive maintenance can also save significant costs that can occur in lost output by preventing manufacturing line downtime. Predictive maintenance is proven to be quite important to the projects, even though it is still in its early phases, by delivering a new supply of data for both original equipment manufacturers and end-users. Motors and their equipment, such as motor controllers and bearings, require proactive maintenance to ensure their safety.
The mining industry deals with the extraction of valuable minerals as well as other geological elements. The extracted minerals are converted into a mineralized state that benefits the miner or prospector. Metals production, metals trading, and metals investing are all common operations in the mining business. There are numerous machineries that are utilized during the mining process such as large mining trucks, hydraulic mining shovels, large dozers, electric rope shovels, rotary drill rigs, and rock drills, motor graders, and large wheel loaders.
A higher initial cost in data collection and analysis technologies, as well as installation, is required for continuous monitoring. System engineering and installation, field instrumentation, such as sensors, cabling, and monitoring and diagnostic system, namely hardware and software, installation, software licenses, user training, and customer support, if necessary, system maintenance for sensor replacement and software updates, as well as required external expertise and support are all considered when calculating the total cost of deploying the system. These services, software, and equipment are expensive, and they require certain skill sets to operate. As a result, operators must spend greater resources in the motor control process, training, and maintenance.

Based on Offering, the market is segmented into Hardware, Software, and Services. In 2020, the software segment registered a substantial revenue share of the motor monitoring market. Software is one of the most important parts of motor monitoring devices. For instance, the way a motor reacts to vibration could reveal the existence of an error, and maintenance is required. The software detects the frequency and intensity of the vibrations caused by wear on parts that can be examined to pre-detect developing faults in components of the motor. Moreover, the software also conveys the user’s action to the hardware, due to which, the device works. In addition, the increasing growth of this segment is owing to instant and precise measurements and display of any potential fault.
Based on End User, the market is segmented into Oil & Gas, Aerospace & Defense, Power Generation, Water & wastewater Treatment, Chemical, Food & Beverages, Metals & Mining, and Others. In 2020, the power generation segment recorded a significant revenue share of the motor monitoring market. The growing demand for renewable energy is fueling the growth of this segment. Motor monitoring solutions facilitate the process of power generation by eliminating delays that can be caused by a sudden motor failure. Aside from the inconvenience, a failure might have disastrous financial and environmental consequences. To prevent these disasters, the power generation industry is significantly employing motor monitoring solutions.
Based on Monitoring Process, the market is segmented into Online and Offline/Portable. In 2020, the Offline motor monitoring segment held the second-largest revenue share of the motor monitoring market. The Offline mode of inspecting the condition of a motor allows the investigator to go through a more elaborated analysis of the motor. Moreover, in-person monitoring also eliminates the requirement of robust internet connectivity. Hence, more people are preferring offline motor monitoring.
Based on Deployment, the market is segmented into On-premise and Cloud. In 2020, the on-premise segment witnessed the largest revenue share of the motor monitoring market. The typical method of deploying motor monitoring services across an organization is through an on-premise deployment. The on-premises solution is deployed locally on the organization’s motors, bearings, shafts, computers, and servers. When businesses choose on-premises solutions, they have complete control over their data because it is physically secured in their facilities. some of the other advantages of the on-premise motor monitoring deployment are increased control over the entire monitoring system as it allows the company to manage the hardware and software platform as well as collected data. In addition, it reduces the company's reliance on external elements like the network and third-party vendors.
Based on Regions, the market is segmented into North America, Europe, Asia Pacific, and Latin America, Middle East & Africa. In 2020, North America accounted for the largest revenue share of the motor monitoring market. The regional market is growing due to the growth of the food and beverages industry of the region. The utilization of motor monitoring solutions in the food and beverages industry across this region is increasing, especially, in the processed food industry. There is a significant number of machineries that are used in the food processing procedure.
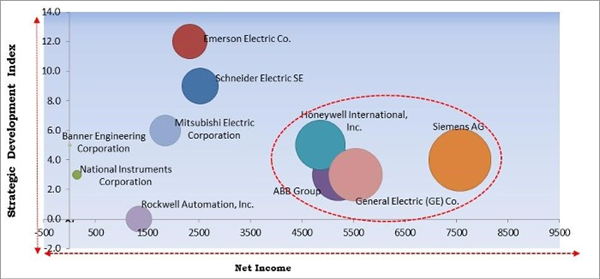
The major strategies followed by the market participants are Product Launches. Based on the Analysis presented in the Cardinal matrix; ABB Group, Honeywell International, Inc., General Electric (GE) Co., and Siemens AG are the forerunners in the Motor Monitoring Market. Companies such as Schneider Electric SE, Rockwell Automation, Inc., Mitsubishi Electric Corporation are some of the key innovators in the Market.
The market research report covers the analysis of key stake holders of the market. Key companies profiled in the report include ABB Group, Honeywell International, Inc., Schneider Electric SE, Emerson Electric Co., Mitsubishi Electric Corporation, Siemens AG, Rockwell Automation, Inc., General Electric (GE) Co., National Instruments Corporation, and Banner Engineering Corporation.
By Offering
By End User
By Monitoring Process
By Deployment
Motor condition monitoring is a system that uses data collected from electric motors and rotating equipment to identify flaws before their occurrence. Rotating machinery and electric motors are the devices that consume the most electricity. Motor monitoring allows for the prediction of potential motor failures and the intervention of the failure in advance. Condition monitoring helps to avoid unplanned downtime while also increasing the energy economy. Additionally, motor condition monitoring also prevents the cost that occurs in unnecessary maintenance of the motor.
Condition-based maintenance majorly focuses on preventing excess downtime, asset failures, and wasteful practices by monitoring the health of the motor to identify what maintenance needs to be performed and when. Any predictive maintenance approach is expected to be incomplete without it. Motor monitoring makes sure that maintenance is only being undertaken when particular thresholds are met or indicators exhibit symptoms of declining performance or impending failure.
Predicting impending motor breakdowns necessitates knowledge, experience, and the use of as many tools as possible. The more tools a technician has and knows how to utilize, the more equipped they is expected to be to estimate the longevity and health of the motor. Online monitoring and offline testing are two aspects of motor monitoring that must be examined and completely utilized in order to acquire an adequate diagnosis of the motor's condition.
The motor itself contains a variety of components that must be precisely tested, including insulation systems, copper winding wire, bearings, and other electrical and mechanical elements. The insulation system comprises very thin insulation produced onto the magnet wire or winding while the ground-wall insulation safeguards the magnet wire in the slots. Off-line testing equipment can accurately analyze the health of these insulation systems, and when the data is appropriately displayed, it can help in anticipating the motor's ability to remain in operation, as well as the requirement of any type of maintenance in the motor.
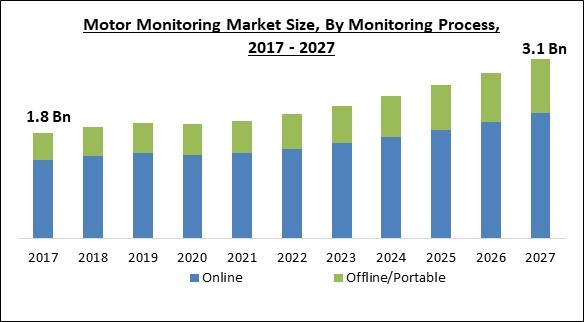
COVID-19 Impact Analysis
The outbreak of the COVID-19 pandemic severely impacted worldwide economies. The closure of various plants and factories, due to lockdowns that were enforced by governments to regulate the spread of the infection, had a severe impact on supply chains across the world, negatively affecting manufacturing, delivery schedules, and product supply. Various companies already stated that there may be delays in product deliveries and a drop in future production. Additionally, worldwide travel prohibitions implemented by various countries across all the regions are affecting opportunities for commercial cooperation and partnerships.
In addition, the pandemic also harmed the motor monitoring industry in a severe manner. Governments and municipal agencies imposed stringent regulations, due to which all non-essential activities were halted. Due to a lack of focus on the development of end-user industries, this had a negative impact on motor monitoring.
Market Growth Factors:
Rising demand for predictive analytics and maintenance
Predictive maintenance is becoming more widely recognized as one of the more easily controllable digitalization applications. Predictive maintenance is a technique for forecasting when equipment will fail and repairing or changing the component before it breaks. This helps to reduce downtime and extend the life of components. Predictive maintenance can also save significant costs that can occur in lost output by preventing manufacturing line downtime. Predictive maintenance is proven to be quite important to the projects, even though it is still in its early phases, by delivering a new supply of data for both original equipment manufacturers and end-users. Motors and their equipment, such as motor controllers and bearings, require proactive maintenance to ensure their safety.
The increasing emergence of the mining industry
The mining industry deals with the extraction of valuable minerals as well as other geological elements. The extracted minerals are converted into a mineralized state that benefits the miner or prospector. Metals production, metals trading, and metals investing are all common operations in the mining business. There are numerous machineries that are utilized during the mining process such as large mining trucks, hydraulic mining shovels, large dozers, electric rope shovels, rotary drill rigs, and rock drills, motor graders, and large wheel loaders.
Market Restraining Factors
Increased payback duration on investment
A higher initial cost in data collection and analysis technologies, as well as installation, is required for continuous monitoring. System engineering and installation, field instrumentation, such as sensors, cabling, and monitoring and diagnostic system, namely hardware and software, installation, software licenses, user training, and customer support, if necessary, system maintenance for sensor replacement and software updates, as well as required external expertise and support are all considered when calculating the total cost of deploying the system. These services, software, and equipment are expensive, and they require certain skill sets to operate. As a result, operators must spend greater resources in the motor control process, training, and maintenance.

Offering Outlook
Based on Offering, the market is segmented into Hardware, Software, and Services. In 2020, the software segment registered a substantial revenue share of the motor monitoring market. Software is one of the most important parts of motor monitoring devices. For instance, the way a motor reacts to vibration could reveal the existence of an error, and maintenance is required. The software detects the frequency and intensity of the vibrations caused by wear on parts that can be examined to pre-detect developing faults in components of the motor. Moreover, the software also conveys the user’s action to the hardware, due to which, the device works. In addition, the increasing growth of this segment is owing to instant and precise measurements and display of any potential fault.
End User Outlook
Based on End User, the market is segmented into Oil & Gas, Aerospace & Defense, Power Generation, Water & wastewater Treatment, Chemical, Food & Beverages, Metals & Mining, and Others. In 2020, the power generation segment recorded a significant revenue share of the motor monitoring market. The growing demand for renewable energy is fueling the growth of this segment. Motor monitoring solutions facilitate the process of power generation by eliminating delays that can be caused by a sudden motor failure. Aside from the inconvenience, a failure might have disastrous financial and environmental consequences. To prevent these disasters, the power generation industry is significantly employing motor monitoring solutions.
Monitoring Process Outlook
Based on Monitoring Process, the market is segmented into Online and Offline/Portable. In 2020, the Offline motor monitoring segment held the second-largest revenue share of the motor monitoring market. The Offline mode of inspecting the condition of a motor allows the investigator to go through a more elaborated analysis of the motor. Moreover, in-person monitoring also eliminates the requirement of robust internet connectivity. Hence, more people are preferring offline motor monitoring.
Deployment Outlook
Based on Deployment, the market is segmented into On-premise and Cloud. In 2020, the on-premise segment witnessed the largest revenue share of the motor monitoring market. The typical method of deploying motor monitoring services across an organization is through an on-premise deployment. The on-premises solution is deployed locally on the organization’s motors, bearings, shafts, computers, and servers. When businesses choose on-premises solutions, they have complete control over their data because it is physically secured in their facilities. some of the other advantages of the on-premise motor monitoring deployment are increased control over the entire monitoring system as it allows the company to manage the hardware and software platform as well as collected data. In addition, it reduces the company's reliance on external elements like the network and third-party vendors.
Regional Outlook
Based on Regions, the market is segmented into North America, Europe, Asia Pacific, and Latin America, Middle East & Africa. In 2020, North America accounted for the largest revenue share of the motor monitoring market. The regional market is growing due to the growth of the food and beverages industry of the region. The utilization of motor monitoring solutions in the food and beverages industry across this region is increasing, especially, in the processed food industry. There is a significant number of machineries that are used in the food processing procedure.
Cardinal Matrix - Motor Monitoring Market Competition Analysis
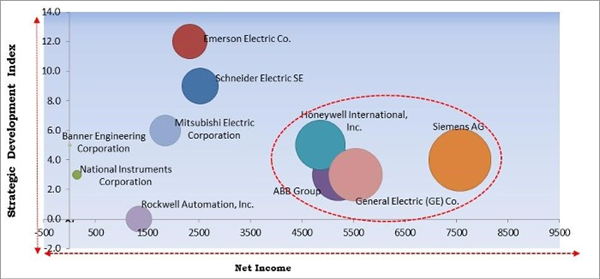
The major strategies followed by the market participants are Product Launches. Based on the Analysis presented in the Cardinal matrix; ABB Group, Honeywell International, Inc., General Electric (GE) Co., and Siemens AG are the forerunners in the Motor Monitoring Market. Companies such as Schneider Electric SE, Rockwell Automation, Inc., Mitsubishi Electric Corporation are some of the key innovators in the Market.
The market research report covers the analysis of key stake holders of the market. Key companies profiled in the report include ABB Group, Honeywell International, Inc., Schneider Electric SE, Emerson Electric Co., Mitsubishi Electric Corporation, Siemens AG, Rockwell Automation, Inc., General Electric (GE) Co., National Instruments Corporation, and Banner Engineering Corporation.
Recent Strategies Deployed in Motor Monitoring Market
Partnerships, Collaborations and Agreements:
- Sep-2021: Honeywell came into a partnership with Ultium Cells, a joint venture that mass-produced battery cells for electric vehicles. This partnership aimed to ensure the quality & integrity of the lithium-ion batteries produced at the company's new manufacturing plant.
- May-2021: Banner Engineering entered into a partnership with Amazon Web Services, a subsidiary of Amazon providing on-demand cloud computing platforms & APIs. This partnership aimed to expand the range of IoT solutions in the AWS market. These solutions include Banner’s DXM series wireless controller & sensors for vibration monitoring on pumps & motors. In addition, this is expected to bridge a gap between plant machinery & the cloud.
- Apr-2021: Siemens entered into a partnership with Toyota Industries, a manufacturer of automatic looms. By this partnership, both the companies is expected to develop AI capable to predict product abnormalities in aluminum die casting. This partnership is aimed at the growth of Siemens by more adoption of their automation & digitalization solution.
- Oct-2020: Schneider Electric partnered with Semiotic Labs, a provider of an AI-driven predictive maintenance solution for AC motors and rotating equipment. The partnership is expected to broaden the company's managed service offering to support the monitoring of rotating equipment that includes pumps, conveyors, induction motors & compressors.
- Mar-2020: Siemens teamed up with the NEC Corporation, a Japanese multinational information technology & Electronics Corporation. This collaboration aimed to provide monitoring & analysis solution for manufacturing which is expected to connect MindSphere from Siemens and NEC's System Invariant Analysis Technology (SIAT). In addition, the collaboration is expected to allow both the companies to provide total data collection, monitoring, storage, and analysis that include customization according to customer requirements.
Acquisitions and Mergers:
- May-2020: Schneider Electric took over ProLeiT, a medium-sized IT company. By this acquisition, the company aimed to expand its portfolio & reinforce its commitment to holistic and software-supported automation. Additionally, ProLeiT is expected to provide Process Control Systems (PCS) with an integrated Manufacturing Execution System (MES) functions optimized for the Customer Packed Goods market that includes the Chemicals, Food and Beverage & Life Sciences segments.
Product Launches and Product Expansions:
- Feb-2022: ABB India introduced the latest series of electrical measuring & power monitoring meters. The new series enables the company to offer a comprehensive portfolio along with the currently offered range of single, multifunction meters & network analyzers, catering to the Panel Meter market in various industries like infrastructure, healthcare, hospitality, and food & beverage.
- Oct-2021: Honeywell launched Searchline Excel Plus and Searchline Excel Edge. The product is capable to deliver continuous monitoring for dangerous gases even in the rain, fog, snow, and other inclement weather which helps facilities to keep their oil and gas, chemical, petrochemical, and other workers and industrial sites safe and gives plant operators peace of mind knowing that their gas detection system can withstand various outdoor conditions.
- Oct-2021: Schneider Electric introduced the latest version of EcoStruxure Power, the flagship power distribution system. The expansion aimed to digitize & simplify electrical distribution infrastructure that delivers reliable always-on power for commercial buildings & infrastructure. In addition, this version is expected to serve with enhanced cybersecurity features, better connectivity & predictive analytics for reducing electrical fires & ensuring the safety of equipment & personnel.
- Apr-2021: GE Digital expanded SmartSignal predictive maintenance software solution by adding new features into it. The added feature consists of unique time-of-action analytics for predicting when any mishappening may occur, enhancing visualization & analyzing tools along with the continued expansion of the Digital Twin Analytics & Content Catalog.
- Sep-2020: Banner Engineering introduced SmartSolutions, a new business unit. The new unit is expected to feature easy-to-install integrated and customizable IIOT kits of wireless solutions, sensors & LED lighting. The product is expected to combine industrially-engineered products in the best possible way to establish savings & success, as well as scale with complete confidence in both the equipment & the manufacturer.
- Jan-2020: Emerson introduced RXi industrial display & panel PC products. The launch aimed to enable consumers to get the same experience look and feel, irrespective of size or application. The product is developed to work with the company's programmable logic control (PLC), programmable automation control (PAC) solutions as well as third-party control systems and monitor, visualize and improve everyday production processes in life sciences, metals and mining, power, and water, and manufacturing and machinery.
Scope of the Study
Market Segments Covered in the Report:
By Offering
- Hardware
- Software, and
- Services
By End User
- Oil & Gas
- Aerospace & Defense
- Power Generation
- Water & wastewater Treatment
- Chemical
- Food & Beverages
- Metals & Mining, and
- Others
By Monitoring Process
- Online and
- Offline/Portable
By Deployment
- On-premise
- Cloud
By Geography
- North America
- US
- Canada
- Mexico
- Rest of North America
- Europe
- Germany
- UK
- France
- Russia
- Spain
- Italy
- Rest of Europe
- Asia Pacific
- China
- Japan
- India
- South Korea
- Singapore
- Malaysia
- Rest of Asia Pacific
- LAMEA
- Brazil
- Argentina
- UAE
- Saudi Arabia
- South Africa
- Nigeria
- Rest of LAMEA
Key Market Players
List of Companies Profiled in the Report:
- ABB Group
- Honeywell International, Inc.
- Schneider Electric SE
- Emerson Electric Co.
- Mitsubishi Electric Corporation
- Siemens AG
- Rockwell Automation, Inc.
- General Electric (GE) Co.
- National Instruments Corporation
- Banner Engineering Corporation
Unique Offerings from the Publisher
- Exhaustive coverage
- The highest number of market tables and figures
- Subscription-based model available
- Guaranteed best price
- Assured post sales research support with 10% customization free
Table of Contents
Chapter 1. Market Scope & Methodology
Chapter 2. Market Overview
Chapter 3. Competition Analysis - Global
Chapter 4. Global Motor Monitoring Market by Offering
Chapter 5. Global Motor Monitoring Market by End User
Chapter 6. Global Motor Monitoring Market by Monitoring Process
Chapter 7. Global Motor Monitoring Market by Deployment
Chapter 8. Global Motor Monitoring Market by Region
Chapter 9. Company Profiles